中国经历了一个发达的青铜礼器铸作和使用的阶段,这是其它国家所没有的。现有的资料表明,到晚商时候,殷墟青铜器的陶范铸造生产工艺流程已经基本规范化。对这一过程进行详细地研究,可以揭示先秦青铜生产的技术水平与组织管理,进而了解中国青铜时代进行陶范铸造的技术选择的深层动因。
一 陶范铸造的工艺流程
所谓陶范铸造,是将金属熔炼成符合一定成分要求的液体并倾倒入预先制好的陶质铸型中,经冷却凝固、清整处理后得到有预定几何形状和物理化学性能的器件的工艺过程,这是是一个复杂的多工艺过程,其典型工序流程如下:
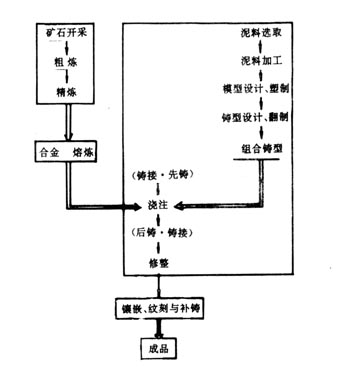
图1 青铜器铸造工序流程(引自《中国上古金属技术》)
殷墟铸铜遗址从未发现炼炉和炼渣,表明冶炼和铸造工艺是分地进行的。因此,安阳的青铜生产工序不包括上图的左边第一个方框里的矿石开采和粗炼,但不排除有精炼的工序。由上图可见,在浇注开始之前,制备陶范的工序和熔炼合金的工序是同步进行的。以下我们概述各个环节的具体做法(铸型的制作部分详见即将发表于《考古》的《殷墟青铜礼器铸型制作工艺》,本文从简)。
(一) 铸型的制作
1、造型材料的选取和制备
这一步骤即图1所示的泥料选取和泥料加工工序。
为了解殷墟时期造型材料的选择和制备工艺,必须对铸铜遗址出土的陶范进行科学检测。迄今为止,殷墟已发现的几处较大的铸铜遗址中,只有苗圃北地和孝民屯东南地出土的部分陶范做了较为详细的检测。检测结果表明:殷墟陶范采用当地的粘土,经淘洗、练泥、陈腐的工序进行处理,并添加河砂、蚌粉(或其它硅酸盐物质)、植物质等羼和料,主要是为增加陶范的耐热急变性能,改善铸造性能。相比而言,芯中含更多羼和料,以具有更好的耐热度和溃散性。陶范添加的羼和料的数量多于陶器,这可能与铸造性能的要求有关。陶范的分型面上有刷涂红色细泥浆或者烟熏的现象,可能是为提高表面质量所采取的举措。
必须指出,究竟使用何种粘土,是地下的生土,还是河流的沉积土,一直存在讨论。而使用化学方法进行分析,难以得出直接的结论。目前笔者正在与威斯康辛大学的Jim Stoltman教授合作,利用偏光显微镜分析陶范的物理结构,了解原材料的选择和孱和料的添加等工艺。从某种意义上说,这样的做法更便于恢复历史的本真。先民们在对材料进行改性的时候,首先看到是它的物理性能的变化。比如淘洗,主要目的就是提高含泥量,虽然化学分析显示氧化钙有降低,但这不是古人的目的。换言之,可以通过氧化钙的降低的现象反证造型材料可能经过淘洗,特别是面料经过淘洗。
2 铸型的设计和制作
铸型通常是由范、芯以及芯撑组合而成的带有内部空腔的封闭实体,空腔即为待铸物体的形状。范形成器物的外表,芯则形成器物的内腔、孔以及某些中空部分。范与范的结合面谓之分型面。
殷墟铸型的做法是将陶土塑制成模,可能采用了类似陶器的制作工艺,模的形状是按照制范的需要设计的,因此较大器物的模一般是按照不同的部位分别制作,整体模型中不必要的部分会被省略,以节约材料和工时。模上花纹的制作有两种形式,一种是在表面贴附泥片,上面雕刻花纹;一种是在模的表面塑制主体花纹的轮廓,再用朱砂描绘次一级花纹的线条。
用模翻范,在范上剔刻花纹的细部,有些花纹是直接在范上模印或刻制的,如肩部的圆涡纹(如图9),这种做法可视作侯马时期模印法的先声。
安阳陶范有两种做法,即李永迪命名的I式范和II式范。前者分型面上没有榫卯,背部光滑,仅有一个水平或垂直的凸棱,较薄,可能主要在三家庄阶段和殷墟一期使用。I式范中有些花纹范,多为一组较窄的花纹,可能是嵌入外面的陶范使用的。II式范主要在殷墟二期以后使用,它的背部凹凸不平,为指窝按压的痕迹,分型面上有榫卯。
针对不同形状和种类的青铜器,一般是按照垂直和水平两个方向来分范,分范的形式比较复杂,这一问题将另文详述。使用复合范的办法制作高浮雕兽头,即在器物范上留下空腔,在凹槽内放置一块范泥,用活块兽头模压印出兽头,也有可能镶嵌小兽头范。
由于对耐火度、退让性和溃散性的高要求,芯很可能是单独制作的,而并非如石璋如所言是完全用模刮去铸件壁厚制成的,特别是一些大型器物的芯,往往是依托不同部位的范,使用粗砂泥夯筑而成。出土的芯一般呈砖红色,质地较为松散和粗糙,不同于质地细腻的模。足等部位的盲芯往往设有泥芯撑,用以同范配合。形成器物空腔的芯带有芯头,芯头侧面有榫,中心有凹窝,用以同底范配合。带有铭文的泥芯多半是由泥模翻印而来,翻印后的阳文还需经过刻制修整,在字的笔画旁边可见清晰的刻槽。其上顶面带有配合用的凸榫,用以镶嵌到器物泥芯上。
3 铸型的干燥、焙烧和装配
铸型制就的下一工序是干燥,组装之后整体焙烧还是分别焙烧之后组装,还存在不同意见。组装之后还要再次干燥(同时也是预热),方能浇注。
范脱模后,需在背阴处自然干燥(阴干),使水分缓慢而均匀地蒸发,这对控制范的变形,保证其严密性至关紧要。小型铸型可能是在烘范窑中焙烧的,窑形结构与小型陶窑相同。这一步骤的重点在于焙烧工艺,谭德睿曾认为陶范焙烧温度高于850度,笔者和刘歆益合作研究,初步认为焙烧温度可能只有600度左右,远远低于陶器的烧成温度。这也与万家保的复原实验的数据比较接近。
多数铸范都在分型面开设榫卯,用以配合组成铸型。在芯和范之间有时还需要设置金属芯撑。
大型器物需要使用底范,芯和底范是联接在一起的。有些大型器物直接在底面夯筑底范,比如孝民屯发现的大型圆形器物底范
三足器通常在足的上方安放浇口范,其中一足作为浇口,另两足是出气孔,圈足器的浇口也设在足上,底范会做出浇道的部分。
至此,整个铸型制作完成。
(二)合金的熔炼和配制
这个问题是整个铸造流程研究中的薄弱环节,基本上所有的步骤都是推测,并且存在争论。
1 关于熔铜器具的讨论
安阳苗圃北地和孝民屯铸铜遗址均出土大量经高温灼烧的陶质残片,有些表面有高温灼烧的裂痕(图2),有的表面已经釉质化,呈玻璃态,背面有泥条盘筑或者草拌泥的痕迹。以往的学者都认为这就是熔炉的残片,采用内燃式加热。对苗圃北地出土的残片分析显示,除1个样品的烧流层内有较多量的铜外,另外两个样品只有微量的铜,3个样品均有痕量的锡、铅等存在。
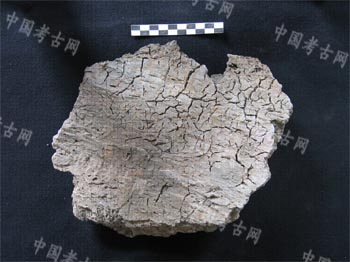
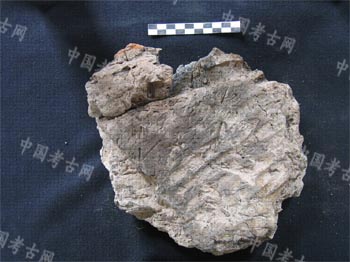
图2 孝民屯东南地铸铜遗址出土的陶质残片(上:正面,下:背面)
笔者曾分析2片这种样品,发现有较高的二氧化硅含量和氧化钙含量,特别是背层,氧化钙含量更高。推测残片的原料很可能是在原生土内加入砂粒和蚌粉得到的。样品背层的烧失量较大,说明还另外加入了植物茎叶,也就是由草拌泥糊成。其中1块样品的焙烧温度高于900℃。有1块样品上附有很少一点铜渣,经检测,含铜、锡、铅三种元素 。
笔者在对安阳孝民屯铸铜遗址出土的大量这种“熔炉”残片进行整理的时候,发现绝大多数残片表面都没有附着金属,即使灼烧得很厉害,表面已接近釉质的样品,从外观上也看不到金属的遗迹,只有少量残片表面粘附有木炭和金属。但是,在苗圃北地和孝民屯铸铜遗址,普遍发现一种表面粘有铜液的残块,有粗砂硬陶和细砂泥质两种,出土时均为小片,不能复原(图3)。此类残片多数有数层衬面,每层衬面均粘有铜液,证明它多次修缮和使用。炉衬表面与铜液接触部分呈灰绿色,且多已烧成了小孔蜂窝状。背面多为较疏松的红烧土。刘屿霞曾多次提到许多红烧土碎片上有炼渣,可能就是这种遗迹 。苗圃北地的发掘者也认为它属于坩埚类的熔铜工具 。
笔者在对安阳孝民屯铸铜遗址出土的大量这种“熔炉”残片进行整理的时候,发现绝大多数残片表面都没有附着金属,即使灼烧得很厉害,表面已接近釉质的样品,从外观上也看不到金属的遗迹,只有少量残片表面粘附有木炭和金属。但是,在苗圃北地和孝民屯铸铜遗址,普遍发现一种表面粘有铜液的残块,有粗砂硬陶和细砂泥质两种,出土时均为小片,不能复原(图3)。此类残片多数有数层衬面,每层衬面均粘有铜液,证明它多次修缮和使用。炉衬表面与铜液接触部分呈灰绿色,且多已烧成了小孔蜂窝状。背面多为较疏松的红烧土。刘屿霞曾多次提到许多红烧土碎片上有炼渣,可能就是这种遗迹 。苗圃北地的发掘者也认为它属于坩埚类的熔铜工具 。
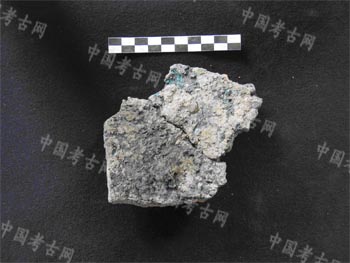
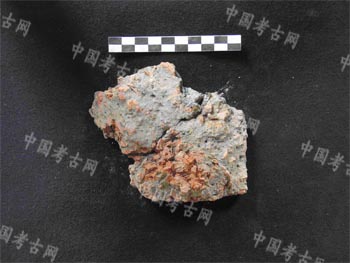
图3 孝民屯东南地铸铜遗址出土坩埚残片(上:正面 下:背面)
这不禁使人产生一种疑问遗址中的“熔炉”和“坩埚”残片到底与金属熔炼是何种关系?
郑州南关外早商铸铜基址出土了一座熔炉的残底,炉的上部残失,只剩一直径约1.60-2.60米的近椭圆形凹坑,坑内填有铜渣、炉壁块、木炭屑、大口尊、坩埚片和红烧土块等。作者推测这是一座熔铜炉,熔铜的工序是先放木炭、次置坩埚、最后再燃火熔铜 。
洛阳北窑西周铸铜遗址出土了近千块的“熔炉残片”,表面烧成龟裂甚至玻璃化,有的还粘有木炭和铜粒,背面有草拌泥的炉圈。但是锅底状的所谓“炉缸”,则内附铜渣两层,材质为红烧土,非常类似于上述的这种坩埚残片 。很难想象,这种不同质地的所谓“炉缸”和“炉圈”属于同一熔炉的不同部分。
北窑铸铜遗址还出土了两座烧窑,窑壁平整垂直,内壁烧结成流状,外壁为红烧土,窑顶封闭,平顶,窑顶中心偏北设一圆筒型烟道(图4)。虽然该窑还属于横穴形的升焰窑,但其燃烧室和烧成室的结构型配置已经接近于马蹄形半倒焰窑,具有较好的加热效果 。发掘报告中并未提及这个烧窑的用途,但很可能与熔炼金属有关,因为如果是烘范窑,通常仅烧到几百度,无法达到让窑壁都烧流的程度。
因此,荆志淳教授和Jim Stoltman教授提出:真正的熔铜器物可能是坩埚,而不是那种陶质熔炉,换言之,是坩埚直接接触金属液,而熔炉则是加热坩埚的器具,这样才能满足浇注时高达1200-1300℃的要求。巴纳先生曾经设想过这样的熔铜器具,陶窑内放置很大的外热式坩埚,埚壁出铜处做得很薄,有管道和窑壁相通,熔化时将管道堵住;铜水化得后,打开管道用棍捅破埚壁,铜水即泻出供浇注用(图5) 。华觉明曾置疑其坩埚的尺寸太大,不能保证合金的熔融,如果坩埚一捅即破,则很难保证其熔炼过程中不会熔穿。尽管存在上述疑问,笔者仍旧认为这种设想有相当大的可能性,因为其能够达到较高的温度,也能解释为何许多熔炉残片表面都没有粘附铜液,它们很可能是窑壁的残片。但是,由于陶质熔炉残片的烧流层也曾检测出多量的铜,因此还不能否认其作为熔炉的可能性。
为此,笔者和Stoltman教授分别提取了大量样品,欲对这两种残片的化学成分、显微结构和制作方法进行详细的分析,荆志淳和岳占伟在安阳着手进行复原实验,测算这种窑炉能够达到的最高温度,以期作进一步的讨论和深入研究。
郑州南关外早商铸铜基址出土了一座熔炉的残底,炉的上部残失,只剩一直径约1.60-2.60米的近椭圆形凹坑,坑内填有铜渣、炉壁块、木炭屑、大口尊、坩埚片和红烧土块等。作者推测这是一座熔铜炉,熔铜的工序是先放木炭、次置坩埚、最后再燃火熔铜 。
洛阳北窑西周铸铜遗址出土了近千块的“熔炉残片”,表面烧成龟裂甚至玻璃化,有的还粘有木炭和铜粒,背面有草拌泥的炉圈。但是锅底状的所谓“炉缸”,则内附铜渣两层,材质为红烧土,非常类似于上述的这种坩埚残片 。很难想象,这种不同质地的所谓“炉缸”和“炉圈”属于同一熔炉的不同部分。
北窑铸铜遗址还出土了两座烧窑,窑壁平整垂直,内壁烧结成流状,外壁为红烧土,窑顶封闭,平顶,窑顶中心偏北设一圆筒型烟道(图4)。虽然该窑还属于横穴形的升焰窑,但其燃烧室和烧成室的结构型配置已经接近于马蹄形半倒焰窑,具有较好的加热效果 。发掘报告中并未提及这个烧窑的用途,但很可能与熔炼金属有关,因为如果是烘范窑,通常仅烧到几百度,无法达到让窑壁都烧流的程度。
因此,荆志淳教授和Jim Stoltman教授提出:真正的熔铜器物可能是坩埚,而不是那种陶质熔炉,换言之,是坩埚直接接触金属液,而熔炉则是加热坩埚的器具,这样才能满足浇注时高达1200-1300℃的要求。巴纳先生曾经设想过这样的熔铜器具,陶窑内放置很大的外热式坩埚,埚壁出铜处做得很薄,有管道和窑壁相通,熔化时将管道堵住;铜水化得后,打开管道用棍捅破埚壁,铜水即泻出供浇注用(图5) 。华觉明曾置疑其坩埚的尺寸太大,不能保证合金的熔融,如果坩埚一捅即破,则很难保证其熔炼过程中不会熔穿。尽管存在上述疑问,笔者仍旧认为这种设想有相当大的可能性,因为其能够达到较高的温度,也能解释为何许多熔炉残片表面都没有粘附铜液,它们很可能是窑壁的残片。但是,由于陶质熔炉残片的烧流层也曾检测出多量的铜,因此还不能否认其作为熔炉的可能性。
为此,笔者和Stoltman教授分别提取了大量样品,欲对这两种残片的化学成分、显微结构和制作方法进行详细的分析,荆志淳和岳占伟在安阳着手进行复原实验,测算这种窑炉能够达到的最高温度,以期作进一步的讨论和深入研究。
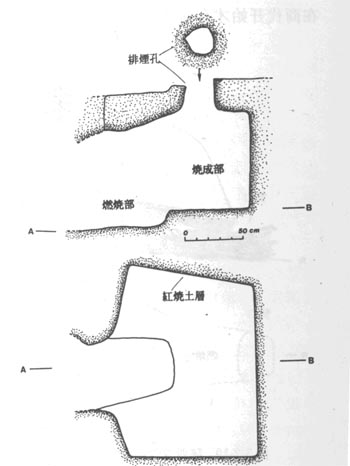
图4 河南洛阳北窑地下升焰式横穴窑
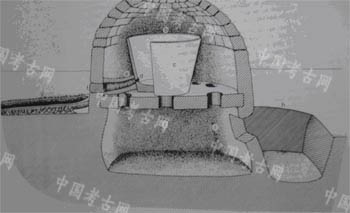
图5 巴纳设想的熔铜窑炉图
2 鼓风
鼓风设施的应用和改进,对于冶金技术的发展至关紧要。
我们在安阳的所有铸铜遗址都发现了陶管(图6),少数陶管表面粘有铜渣,它与铜器铸造有关是勿庸置疑的,侯马铸铜遗址也曾出土类似的遗物,并认为是鼓风的工具 。在周原也有类似的发现。泰利科特的《冶金史》一书中有埃及金匠使用带陶风嘴的吹管的材料(约1460B.C.,如图7)。但是这种陶管的用法可能与这种埃及的吹管有所区别,具体如何使用,目前还不清楚。
鼓风设施的应用和改进,对于冶金技术的发展至关紧要。
我们在安阳的所有铸铜遗址都发现了陶管(图6),少数陶管表面粘有铜渣,它与铜器铸造有关是勿庸置疑的,侯马铸铜遗址也曾出土类似的遗物,并认为是鼓风的工具 。在周原也有类似的发现。泰利科特的《冶金史》一书中有埃及金匠使用带陶风嘴的吹管的材料(约1460B.C.,如图7)。但是这种陶管的用法可能与这种埃及的吹管有所区别,具体如何使用,目前还不清楚。
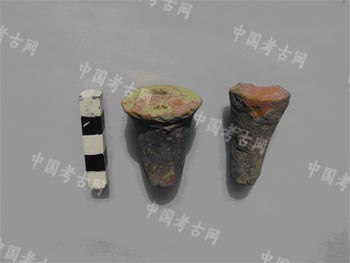
图6 孝民屯东南地铸铜遗址出土陶管
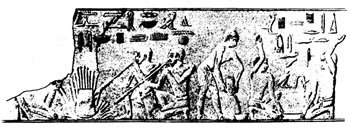
图7 埃及金匠用陶吹管吹火助熔(转引自《中国古代金属技术》,326页,图8-20)
“橐”这种风囊鼓风器,尽管并不知道确切始于何时,却在古书中多有记载。尽管在商代并未发现橐或其他鼓风器的遗存,但是《金文编》附录上11中有“ ” 字,此字一般出现在爵、觚、鼎上,形如皮囊,应为“橐”的古写,又《甲骨文编》中有“ ”字,如同用手提引皮橐,这些都可以作为商代使用皮风囊的佐证。
在清代刘云《矿政辑略》中说,这种鼓风的皮囊,是使用一整张黑山羊的皮缝合,仅在腹部留出小孔,塞入竹筒,深约两三寸。使用的时候,将皮囊套在脚上用脚踩住,一手提住皮头,从上到下按压,则风就会从竹筒中喷出,可用于炊事或者冶炼。这种原始形式的皮风囊,至今仍在许多原始民族中使用,如民族学调查所见的藏族使用的皮囊(图8),由通风管、皮囊和闭合装置组成,操作者用手启闭控制鼓风 。印度也有类似的材料,与藏族使用的非常相似(图9)。这种工具对于小规模熔炼还是很适用的,便携,制作也方便。
在清代刘云《矿政辑略》中说,这种鼓风的皮囊,是使用一整张黑山羊的皮缝合,仅在腹部留出小孔,塞入竹筒,深约两三寸。使用的时候,将皮囊套在脚上用脚踩住,一手提住皮头,从上到下按压,则风就会从竹筒中喷出,可用于炊事或者冶炼。这种原始形式的皮风囊,至今仍在许多原始民族中使用,如民族学调查所见的藏族使用的皮囊(图8),由通风管、皮囊和闭合装置组成,操作者用手启闭控制鼓风 。印度也有类似的材料,与藏族使用的非常相似(图9)。这种工具对于小规模熔炼还是很适用的,便携,制作也方便。
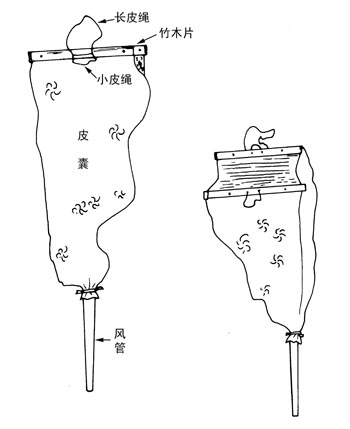
图8 藏族使用的皮囊(转引自王工硕士论文)
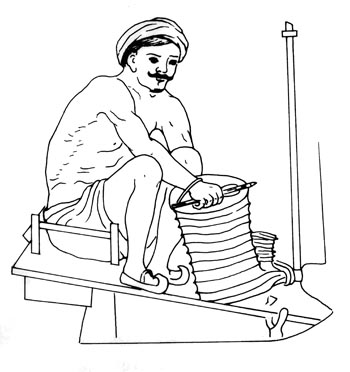
图9 印度使用的气囊
目前还无法确知安阳时期鼓风的器具和作用形式,但是据记载早在战国时期,即已使用多橐鼓风。以安阳当时熔炼合金的温度以及规模而论,很可能已经使用多橐鼓风,并且,商代的鼓风器可能比藏族使用的皮囊还要复杂。
3 合金的配制
商代青铜合金的配制是在专门的铸造场地或者作坊中进行的。到了晚商阶段,已经熟练掌握了铜-锡-铅三元合金的冶炼和熔化技术。当时的工匠对于青铜合金配比与机械性能的关系已经有了相当深入的认识,并且对于操作也有相当严格的控制,已经可以按照不同的用途来有意地采取不同配比的合金。同时,原料的供应是否丰厚,社会风气的变化以及等级身分的尊卑,都可能对青铜器的合金配比造成影响。
但是,迄今为止,殷墟青铜器的合金配制的工艺问题尚未得到解决。苗圃北地铸铜遗址曾出土了一件长方形铜块,有学者推断其是作为铸造青铜器的备用料 。这块铜块究竟是人们有意生产的低锡合金锭?还是浇注锡青铜器时多余金属液的结块?此铜块中的锡是人为有意识加入的,还是冶炼含锡铜矿时带入的?仍有待判定。由于没有发现锡锭,故殷墟出土的大量锡青铜器是如何合金化的,尚需进一步研究。殷墟小屯村E16坑曾出土有2块铅锭。2块铅锭的金属部分含高纯量的铅及微量锌、砷 。铅锭的存在表明是用金属铅直接配制青铜合金的。。近年来安阳在一处商代水井中发现一件椭圆形的大金属块,对其进行分析检测,将对此问题有所帮助。
商代青铜合金的配制是在专门的铸造场地或者作坊中进行的。到了晚商阶段,已经熟练掌握了铜-锡-铅三元合金的冶炼和熔化技术。当时的工匠对于青铜合金配比与机械性能的关系已经有了相当深入的认识,并且对于操作也有相当严格的控制,已经可以按照不同的用途来有意地采取不同配比的合金。同时,原料的供应是否丰厚,社会风气的变化以及等级身分的尊卑,都可能对青铜器的合金配比造成影响。
但是,迄今为止,殷墟青铜器的合金配制的工艺问题尚未得到解决。苗圃北地铸铜遗址曾出土了一件长方形铜块,有学者推断其是作为铸造青铜器的备用料 。这块铜块究竟是人们有意生产的低锡合金锭?还是浇注锡青铜器时多余金属液的结块?此铜块中的锡是人为有意识加入的,还是冶炼含锡铜矿时带入的?仍有待判定。由于没有发现锡锭,故殷墟出土的大量锡青铜器是如何合金化的,尚需进一步研究。殷墟小屯村E16坑曾出土有2块铅锭。2块铅锭的金属部分含高纯量的铅及微量锌、砷 。铅锭的存在表明是用金属铅直接配制青铜合金的。。近年来安阳在一处商代水井中发现一件椭圆形的大金属块,对其进行分析检测,将对此问题有所帮助。
(三)浇注
浇注是将熔融的铜合金注入铸型型腔的过程。为了提高充型能力,可能采用了预热铸型、过热浇注和配制充型力强的合金等措施。
预热铸型是提高充型能力的措施之一,万家保在复原试铸商代青铜器时将铸型预热到300-400℃ ,冯富根等则预热至400-500℃,浇注时的铸型温度在200~300℃ ,均得到了较满意的结果。
无论是纯铜还是铜合金,液态温度越高,流动性越好,充型能力越强,反之则相反。因之,浇注温度要高于熔点。现代铸造工艺将这个温度差称之为过热温度 。殷商铸铜的浇注温度尚未见诸测定报告。万家保复原试铸时的熔化温度为1350℃ ,冯富根等试铸时的熔化温度为1200℃、浇注温度在1100~1200℃ 。根据洛阳北窑西周铸铜遗址熔炉温度为1200~1250℃ ,可知冯富根等人的试铸更接近于真实情况。另外,过热温度越高,铜合金的吸气能力越大,易使铸件生成气孔。因此,过热温度的掌握应恰到好处。
小型器物当是用浇包来浇铸的,大型铜器则可能使用浇包和槽道浇注。苗圃北地铸铜遗址出土了一座半地穴式的工棚,底部安放有大型的长方形底范,如前图16所示,同时残存几条有流向的灰色发亮的流面,据推测是铜液流经的槽道。透过这些现象可以猜测,如果将浇包安放在当时的地面上,铸造时捅开,铜液即可由槽道而注入安于棚底的铸型 。孝民屯铸铜遗址出土的大型圆形器物底范也位于半地穴的F43内,说明这种猜测是有道理的。大型器物铸造时有可能已采用《天工开物》所载槽注法,采用四到八个浇包同时槽注。
浇注是将熔融的铜合金注入铸型型腔的过程。为了提高充型能力,可能采用了预热铸型、过热浇注和配制充型力强的合金等措施。
预热铸型是提高充型能力的措施之一,万家保在复原试铸商代青铜器时将铸型预热到300-400℃ ,冯富根等则预热至400-500℃,浇注时的铸型温度在200~300℃ ,均得到了较满意的结果。
无论是纯铜还是铜合金,液态温度越高,流动性越好,充型能力越强,反之则相反。因之,浇注温度要高于熔点。现代铸造工艺将这个温度差称之为过热温度 。殷商铸铜的浇注温度尚未见诸测定报告。万家保复原试铸时的熔化温度为1350℃ ,冯富根等试铸时的熔化温度为1200℃、浇注温度在1100~1200℃ 。根据洛阳北窑西周铸铜遗址熔炉温度为1200~1250℃ ,可知冯富根等人的试铸更接近于真实情况。另外,过热温度越高,铜合金的吸气能力越大,易使铸件生成气孔。因此,过热温度的掌握应恰到好处。
小型器物当是用浇包来浇铸的,大型铜器则可能使用浇包和槽道浇注。苗圃北地铸铜遗址出土了一座半地穴式的工棚,底部安放有大型的长方形底范,如前图16所示,同时残存几条有流向的灰色发亮的流面,据推测是铜液流经的槽道。透过这些现象可以猜测,如果将浇包安放在当时的地面上,铸造时捅开,铜液即可由槽道而注入安于棚底的铸型 。孝民屯铸铜遗址出土的大型圆形器物底范也位于半地穴的F43内,说明这种猜测是有道理的。大型器物铸造时有可能已采用《天工开物》所载槽注法,采用四到八个浇包同时槽注。
(四)铸后加工
《荀子•疆国篇》称“刑范正、金锡美、工冶巧、火齐得,剖刑则莫邪已。 然而不剥脱,不砥厉,则不可以断绳。剥脱之,砥厉之,则蠡盘盂,刎牛马,忽然耳。”这一段话不仅特指铜剑铸作,于先秦青铜器制作亦有比较普遍的意义。他把器件铸作明确地分成铸造、铸后加工两阶段。
其中,前四句概括了古代青铜器冶铸工艺的四个要素,意为:铸型必须形制端正、尺寸准确,要用优质的铜锡配制合金,匠师具有熟练的技巧,合金的熔炼、浇注均要火候得当。这体现了先秦时期人们对于冶铸技术要诀的理解,为人们多所援引。但是,后一段被提及的比例远远低于前者,说明人们没有将铸后加工置于应有的重要地位。事实上,铸后加工对于器件的最终质量具有关键的作用,通常包括脱范、清理、磨砺等。脱范后有局部缺损的铸件还需补缀。
器物铸成冷却后,用力敲打即可去除铸范,泥芯因附着器内,较难去除,需要使用工具将其剔凿出来。然后使用锤击、锯截、錾凿和刮削等手法,以去除浇口、飞边、毛刺和多肉等。所用的工具包括一些金属器具,比如铜削、铜刻针等。
殷墟青铜器的补缀分为两种,一种是所谓熔补,即直接以熔融铜液倾倒在需补缀的孔洞或裂隙上;另一种是补铸,如果青铜器的一部分或附件,如足或等,由于种种原因未铸成或断折,则需在残体上做范,再经浇注与器体熔接而成。
铸坯变为成品、具有较好的外观,磨砺起着重要的作用。许多青铜礼器上的磨痕现仍清晰可辨,应是用粗细砺石逐道加工而成。孝民屯铸铜遗址就出土了数千块磨石,大小、厚薄、形状不一,质料有粗、细砂岩两种,用之打磨修整铜器的表面,也说明该道工序的工作量之大。殷墟铸铜遗址中木炭往往与砺石同出,在磨光之后,有可能使用木炭在水中打磨器物,使铜器发亮 。
那么,铸后加工的工作量到底在铸作过程中占有多大的比重呢?由于缺少记载,仅凭出土实物和冶铸遗存的情况难以得到确证。华觉明根据史贻直、德成等于乾隆二十四年编纂的《钦定工部则例九十五卷》的记载进行了统计和计算,用拨蜡法制作爵、等礼器,铸造阶段用工量仅为用工总量的4.20%~5.30%。如以铸造用工量为1,则前期准备的用工量是7.07~8.92,铸后用工的加工量高达10.29~15.09。即使除却镟里合口、年号镌刻、烧古诸项商周青铜器没有的工艺,仍然高达6.29~10.18 。由此推测:商代青铜礼器形制复杂,又仅用铜质、石质工具进行操作,依器件复杂程度不同大概接近6~10的范畴,象司母戊鼎、司母辛鼎这样的大件,或者还需更多。
也许正因为铸后加工如此繁复,才迫使铸师们代复一代地想方设法改进工艺,殷墟青铜礼器铸造工艺的发达、铸铜工序的严格可能与此不无干系。在一定条件下,不利因素之逼迫正是促进工艺更替的重要动因。理解这一点,将有助于我们理解技术演进的本质及有关因素相生相克、相辅相成的辩证关系。
《荀子•疆国篇》称“刑范正、金锡美、工冶巧、火齐得,剖刑则莫邪已。 然而不剥脱,不砥厉,则不可以断绳。剥脱之,砥厉之,则蠡盘盂,刎牛马,忽然耳。”这一段话不仅特指铜剑铸作,于先秦青铜器制作亦有比较普遍的意义。他把器件铸作明确地分成铸造、铸后加工两阶段。
其中,前四句概括了古代青铜器冶铸工艺的四个要素,意为:铸型必须形制端正、尺寸准确,要用优质的铜锡配制合金,匠师具有熟练的技巧,合金的熔炼、浇注均要火候得当。这体现了先秦时期人们对于冶铸技术要诀的理解,为人们多所援引。但是,后一段被提及的比例远远低于前者,说明人们没有将铸后加工置于应有的重要地位。事实上,铸后加工对于器件的最终质量具有关键的作用,通常包括脱范、清理、磨砺等。脱范后有局部缺损的铸件还需补缀。
器物铸成冷却后,用力敲打即可去除铸范,泥芯因附着器内,较难去除,需要使用工具将其剔凿出来。然后使用锤击、锯截、錾凿和刮削等手法,以去除浇口、飞边、毛刺和多肉等。所用的工具包括一些金属器具,比如铜削、铜刻针等。
殷墟青铜器的补缀分为两种,一种是所谓熔补,即直接以熔融铜液倾倒在需补缀的孔洞或裂隙上;另一种是补铸,如果青铜器的一部分或附件,如足或等,由于种种原因未铸成或断折,则需在残体上做范,再经浇注与器体熔接而成。
铸坯变为成品、具有较好的外观,磨砺起着重要的作用。许多青铜礼器上的磨痕现仍清晰可辨,应是用粗细砺石逐道加工而成。孝民屯铸铜遗址就出土了数千块磨石,大小、厚薄、形状不一,质料有粗、细砂岩两种,用之打磨修整铜器的表面,也说明该道工序的工作量之大。殷墟铸铜遗址中木炭往往与砺石同出,在磨光之后,有可能使用木炭在水中打磨器物,使铜器发亮 。
那么,铸后加工的工作量到底在铸作过程中占有多大的比重呢?由于缺少记载,仅凭出土实物和冶铸遗存的情况难以得到确证。华觉明根据史贻直、德成等于乾隆二十四年编纂的《钦定工部则例九十五卷》的记载进行了统计和计算,用拨蜡法制作爵、等礼器,铸造阶段用工量仅为用工总量的4.20%~5.30%。如以铸造用工量为1,则前期准备的用工量是7.07~8.92,铸后用工的加工量高达10.29~15.09。即使除却镟里合口、年号镌刻、烧古诸项商周青铜器没有的工艺,仍然高达6.29~10.18 。由此推测:商代青铜礼器形制复杂,又仅用铜质、石质工具进行操作,依器件复杂程度不同大概接近6~10的范畴,象司母戊鼎、司母辛鼎这样的大件,或者还需更多。
也许正因为铸后加工如此繁复,才迫使铸师们代复一代地想方设法改进工艺,殷墟青铜礼器铸造工艺的发达、铸铜工序的严格可能与此不无干系。在一定条件下,不利因素之逼迫正是促进工艺更替的重要动因。理解这一点,将有助于我们理解技术演进的本质及有关因素相生相克、相辅相成的辩证关系。
二 讨论
1、两大技术体系的结合
综上所述,殷墟时期青铜器陶范铸造工艺具有非常复杂的生产工序,显示出青铜器的铸造不像陶器、骨器、玉器那样是单一行业独立完成的,而是两大技术体系--制陶和金属冶铸的有机结合,双方互相适应、不断调整的结果。
《墨子•耕柱篇》有云:“陶铸之于昆吾”,指的即是用陶范铸造铜器。在中国古代,“陶冶”、“陶铸”是当然地联系在一起的,这正反映了冶铸与制陶的历史联系。高度发达的中国青铜冶铸技术,其根底是在高度发达的制陶技术之中。具体表现在:许多铜器的形制和纹饰以各种陶器为祖型;铜器的成形由制陶术的模制工艺得到启示;熔炼金属的高温技术来源于制陶业的经验;造型材料的选取和制备、铸型的加工制作技术亦均来自制陶术。
中国青铜器有别于其他地区的特征有三,即器物的形制、纹饰和铭文,这三者与陶器都有着直接关系。比如鼎、簋、觚、爵等主要器形,都可以在陶器中找到它的原型,而二里头时期封顶铜对封顶陶的模仿也是一个突出的例子。云雷纹、兽面纹、夔龙纹也都分别能在彩陶的纹饰中找到祖型。在陶器上刻画符号的思想很可能为铸造业继承而形成铜器上的铭文。
熔炼金属的高温技术来源于制陶业的经验,这一点前面已有详细的讨论。对于制陶业而言,高温技术的突破性改进来自窑炉的发明。烧成温度的高低,气氛性质的好坏,取决于窑炉结构是否合理,也就是取决于窑炉抽吸空气量的多少,窑炉是朝着能控制进窑空气量,提高烧成温度,掌握还原气氛的方向发展的 。竖穴式的升焰窑,火眼的数量和分布非常重要,火眼数量越多,火与陶坯的热交换越均匀,远处的火眼采用放大孔径的办法来弥补火焰压力的不足,以此来达到改善窑内的温度分布状况。火膛越大窑炉升温越快,温度越高 。这些技术都被铸造业继承。采用高温技术(包括对炉气的控制等)改变天然物性质,得到所需要的属性,最先是在陶器烧制中实现的,然后,又由青铜冶铸业所继承和发展。所以,就对自然界的变革和作业性质来说,与其它手工业技术相比,青铜冶铸和制陶有着更紧密的联系。
造型材料的选择和制备技术非常关键。古代陶器质地较致密,气孔率低,氧化铁(Fe203)含量较高,氧化钙(CaO)含量低,一般不采用农耕土和含腐殖质较多的地表土,也不用普通黄土,而是选取红土、沉积土、黑土为原料,有时需掺砂、蚌粉、植物质、陶末等孱和料以减少收缩和改善其耐激冷、激热的性能 。所有这些工艺经验和焙烧规范都在铸型材料的制备中得到了体现。陶范和陶器材料的制作和焙烧工艺的不同显示出制陶部门为提高铸造性能所做的工艺调整。这一点很重要,需要澄清细节。也提醒我们,对金属技术进行研究,还要兼及对陶瓷技术的深入理解。中国绵延的黄土环境,在此基础上新石器时代既已高度发达的制陶技术,直接关系着为何中国青铜时代会选择陶范铸造这样一个工艺系统,而不是锻造或是其它铸造方法。
综上所述,殷墟时期青铜器陶范铸造工艺具有非常复杂的生产工序,显示出青铜器的铸造不像陶器、骨器、玉器那样是单一行业独立完成的,而是两大技术体系--制陶和金属冶铸的有机结合,双方互相适应、不断调整的结果。
《墨子•耕柱篇》有云:“陶铸之于昆吾”,指的即是用陶范铸造铜器。在中国古代,“陶冶”、“陶铸”是当然地联系在一起的,这正反映了冶铸与制陶的历史联系。高度发达的中国青铜冶铸技术,其根底是在高度发达的制陶技术之中。具体表现在:许多铜器的形制和纹饰以各种陶器为祖型;铜器的成形由制陶术的模制工艺得到启示;熔炼金属的高温技术来源于制陶业的经验;造型材料的选取和制备、铸型的加工制作技术亦均来自制陶术。
中国青铜器有别于其他地区的特征有三,即器物的形制、纹饰和铭文,这三者与陶器都有着直接关系。比如鼎、簋、觚、爵等主要器形,都可以在陶器中找到它的原型,而二里头时期封顶铜对封顶陶的模仿也是一个突出的例子。云雷纹、兽面纹、夔龙纹也都分别能在彩陶的纹饰中找到祖型。在陶器上刻画符号的思想很可能为铸造业继承而形成铜器上的铭文。
熔炼金属的高温技术来源于制陶业的经验,这一点前面已有详细的讨论。对于制陶业而言,高温技术的突破性改进来自窑炉的发明。烧成温度的高低,气氛性质的好坏,取决于窑炉结构是否合理,也就是取决于窑炉抽吸空气量的多少,窑炉是朝着能控制进窑空气量,提高烧成温度,掌握还原气氛的方向发展的 。竖穴式的升焰窑,火眼的数量和分布非常重要,火眼数量越多,火与陶坯的热交换越均匀,远处的火眼采用放大孔径的办法来弥补火焰压力的不足,以此来达到改善窑内的温度分布状况。火膛越大窑炉升温越快,温度越高 。这些技术都被铸造业继承。采用高温技术(包括对炉气的控制等)改变天然物性质,得到所需要的属性,最先是在陶器烧制中实现的,然后,又由青铜冶铸业所继承和发展。所以,就对自然界的变革和作业性质来说,与其它手工业技术相比,青铜冶铸和制陶有着更紧密的联系。
造型材料的选择和制备技术非常关键。古代陶器质地较致密,气孔率低,氧化铁(Fe203)含量较高,氧化钙(CaO)含量低,一般不采用农耕土和含腐殖质较多的地表土,也不用普通黄土,而是选取红土、沉积土、黑土为原料,有时需掺砂、蚌粉、植物质、陶末等孱和料以减少收缩和改善其耐激冷、激热的性能 。所有这些工艺经验和焙烧规范都在铸型材料的制备中得到了体现。陶范和陶器材料的制作和焙烧工艺的不同显示出制陶部门为提高铸造性能所做的工艺调整。这一点很重要,需要澄清细节。也提醒我们,对金属技术进行研究,还要兼及对陶瓷技术的深入理解。中国绵延的黄土环境,在此基础上新石器时代既已高度发达的制陶技术,直接关系着为何中国青铜时代会选择陶范铸造这样一个工艺系统,而不是锻造或是其它铸造方法。
2、铸造业的组织和管理
这一条笔者不能展开讨论,因为这本身就是另外一个很复杂的题目,将另文详述。
唐际根以殷墟有承继关系的2000座墓葬为基础,利用统计分析,提出晚商社会是以氏为单位的平行结构,同时具有垂直分布的社会阶层,王室或精英阶层不足不到1%,贵族阶层占7-10%,82-87%的人口属于平民,而最低的阶层只有大约3-7%,这一结果表明商代不是奴隶社会,而以平民为主 。这个发现提醒我们有必要重新考虑工匠的身份问题,进而探讨殷墟冶铸业的组织管理。
根据对甲骨文和金文文献中“工”、“多工”、“百工”等词的释读和辨析,认为殷墟时期的工匠多半具有平民的身份。而殷墟西区墓地以及铸铜遗址出土的工匠墓地研究显示,大部分出工具的墓均规模较小,一般都有棺,或有棺有椁,并有成组的陶器或一两件青铜礼器。这说明这些墓主人生前有一定的生产工具和财富,并有相应的社会地位。他们很可能是“工”的主体,在作坊中从事技术性的工作。从各墓区中墓葬的延续性来看,这些“工”以家族为单位,世守其业,与文献上记载的“工之子恒为工”(《国语•齐语》)一致。商代和西周铜器上多镌刻有族徽,许多都对应着不同的职业,说明在商代开始,各族群的职业明显趋于专一化 。
《左传》定公四年:“昔武王克商,成王定之,分鲁公以……殷民六族:条氏、徐氏、萧氏、索氏、长勺氏,尾勺氏,使帅其宗氏,辑其分族,将其类丑……分康叔以殷民七族:陶氏、施氏、繁氏、 氏、樊氏、饥氏、终葵氏”,这些族的名称被认为与其职业相关,比如陶(陶器)、施(旗帜)、 (炊器)、长勺和尾勺(酒器)、索(绳索)、樊(防护围栏)等 ,索氏器的发现亦证明这些人可能拥有一定的社会地位 。而卜辞关于“左工”,“右工”的记述,也被认为可能存在类似于军队的编制 ,这说明当时是有严格的组织管理的。
根据铭文辨识和有限的考古资料,参考春秋战国时的情况 ,对殷墟铸造业的组织管理作一个可能的推测:殷墟冶铸业的管理似乎也有这样一个三级结构,但是不如战国时期那样规范和严密。
王室成员或高级贵族作为监造者,不参与实际生产,在铭文中常有“××作器”的记载。
“司工”为管理手工业的官员;“多工”为从事管理的下层官吏。
制造者为“工”,具有较高技艺的匠师从事技术设计和操作指挥;工匠,承担大部分的生产活动,可能存在制模、制范和铸器的技术分工,由不同的族众来分别完成;工奴可能来自俘虏、罪人或家奴,从事铸造生产中技术含量较低的繁重体力劳动,比如取土、练泥、焙烧陶范、加热鼓风、搬运以及铸后清理等。
以铸造司母戊大鼎这样重达八百多公斤的铜器为例,运土、备料、制模、制范、制芯、合范、焙烧、合金熔炼、鼓风、浇注、清理、打磨,大概需要上百人同时工作。要这么多人有条不紊地工作,须有高超的管理水平和严格的纪律性。
这一条笔者不能展开讨论,因为这本身就是另外一个很复杂的题目,将另文详述。
唐际根以殷墟有承继关系的2000座墓葬为基础,利用统计分析,提出晚商社会是以氏为单位的平行结构,同时具有垂直分布的社会阶层,王室或精英阶层不足不到1%,贵族阶层占7-10%,82-87%的人口属于平民,而最低的阶层只有大约3-7%,这一结果表明商代不是奴隶社会,而以平民为主 。这个发现提醒我们有必要重新考虑工匠的身份问题,进而探讨殷墟冶铸业的组织管理。
根据对甲骨文和金文文献中“工”、“多工”、“百工”等词的释读和辨析,认为殷墟时期的工匠多半具有平民的身份。而殷墟西区墓地以及铸铜遗址出土的工匠墓地研究显示,大部分出工具的墓均规模较小,一般都有棺,或有棺有椁,并有成组的陶器或一两件青铜礼器。这说明这些墓主人生前有一定的生产工具和财富,并有相应的社会地位。他们很可能是“工”的主体,在作坊中从事技术性的工作。从各墓区中墓葬的延续性来看,这些“工”以家族为单位,世守其业,与文献上记载的“工之子恒为工”(《国语•齐语》)一致。商代和西周铜器上多镌刻有族徽,许多都对应着不同的职业,说明在商代开始,各族群的职业明显趋于专一化 。
《左传》定公四年:“昔武王克商,成王定之,分鲁公以……殷民六族:条氏、徐氏、萧氏、索氏、长勺氏,尾勺氏,使帅其宗氏,辑其分族,将其类丑……分康叔以殷民七族:陶氏、施氏、繁氏、 氏、樊氏、饥氏、终葵氏”,这些族的名称被认为与其职业相关,比如陶(陶器)、施(旗帜)、 (炊器)、长勺和尾勺(酒器)、索(绳索)、樊(防护围栏)等 ,索氏器的发现亦证明这些人可能拥有一定的社会地位 。而卜辞关于“左工”,“右工”的记述,也被认为可能存在类似于军队的编制 ,这说明当时是有严格的组织管理的。
根据铭文辨识和有限的考古资料,参考春秋战国时的情况 ,对殷墟铸造业的组织管理作一个可能的推测:殷墟冶铸业的管理似乎也有这样一个三级结构,但是不如战国时期那样规范和严密。
王室成员或高级贵族作为监造者,不参与实际生产,在铭文中常有“××作器”的记载。
“司工”为管理手工业的官员;“多工”为从事管理的下层官吏。
制造者为“工”,具有较高技艺的匠师从事技术设计和操作指挥;工匠,承担大部分的生产活动,可能存在制模、制范和铸器的技术分工,由不同的族众来分别完成;工奴可能来自俘虏、罪人或家奴,从事铸造生产中技术含量较低的繁重体力劳动,比如取土、练泥、焙烧陶范、加热鼓风、搬运以及铸后清理等。
以铸造司母戊大鼎这样重达八百多公斤的铜器为例,运土、备料、制模、制范、制芯、合范、焙烧、合金熔炼、鼓风、浇注、清理、打磨,大概需要上百人同时工作。要这么多人有条不紊地工作,须有高超的管理水平和严格的纪律性。
三、结语
综上所述,可以得到以下三条结论。
1、殷墟青铜器铸造工艺流程的各个环节均已步入规范化,并达到较高的水平。殷墟铸造业规模的扩大、铜器产量的大幅提高,是建立在工艺流程的规范化、工艺控制的严格性基础上的。
2、必须依托于严格的组织管理,才能完成各个部门之间的协调,使得铜器的复杂化生产过程得以实现。
3、中国青铜时代陶范铸造的工艺选择,是与中国的黄土环境及与之相应的高超的制陶技术密切相关的。
综上所述,可以得到以下三条结论。
1、殷墟青铜器铸造工艺流程的各个环节均已步入规范化,并达到较高的水平。殷墟铸造业规模的扩大、铜器产量的大幅提高,是建立在工艺流程的规范化、工艺控制的严格性基础上的。
2、必须依托于严格的组织管理,才能完成各个部门之间的协调,使得铜器的复杂化生产过程得以实现。
3、中国青铜时代陶范铸造的工艺选择,是与中国的黄土环境及与之相应的高超的制陶技术密切相关的。
(本研究获得国家文物局课题“‘指南针’计划之古代冶金与铸造技术发明创造研究试点”的支持。本文写作过程中,得到王学荣、荆志淳和Jim Stoltman教授的帮助,在此表示诚挚的谢意。)
参考文献:
1、中国社会科学院考古研究所安阳工作队:《2000-2001安阳孝民屯东南地殷代铸铜遗址发掘报告》,《考古学报》2006年3期。对这批材料的检测结果参见刘煜、岳占伟:《殷墟陶范的材料及处理工艺的初步研究》,《夏商周文明研究(六)--2004年安阳殷商文明国际学术研讨会论文集》,社会科学文献出版社,2004,450-456页。后补充数据收入中国社会科学院考古研究所考古科技中心编《科技考古》第1辑,中国社会科学出版社,2005年,226-236页。
2、李永迪, Anyang Foundry : Archaeological Remains, Casting Technology and Production Organization, A thesis for Ph. D to Harvard University,2003.
3、石璋如:《殷代的铸铜工艺》,《历史语言研究所集刊》第26本。
4、谭德睿:《中青铜时代陶范铸造技术研究》,《考古学报》1999年2期,220页。
5、李济、万家保:《殷墟出土五十三件青铜容器之研究》,1972年,台北。
6、刘煜:《殷墟青铜器制作工艺的技术演进》,《21世纪中国考古学与世界考古学》,中国社会科学出版社,2002年,613-631页。
7、华觉明:《中国古代金属技术铜和铁造就的文明》,大象出版社,1999年。
8、刘煜、岳占伟:《殷墟陶范的材料及处理工艺的初步研究》,,中国社会科学院考古研究所考古科技中心编《科技考古》第1辑,中国社会科学出版社,2005年,226-236页。
9、刘屿霞:《殷代冶铜术之研究》,《安阳发掘报告》第四期,1933年,681-696页。
10、中国社会科学院考古研究所编著:《殷墟的发现与研究》,科学出版社,1994年,87页。
11、河南省文物研究所:《郑州商代二里冈期铸铜基址》,《考古学集刊》第6集,中国社会科学出版社,1986年,100-122页。
12、洛阳市文物工作队:《1975-1979年洛阳西周北窑铸铜遗址的发掘》,《考古》1983年5期,430-441页。
13、熊海堂:《东亚窑业技术发展与交流史研究》,南京大学出版社,1995年,57页。
14、N. Barnard, Origins of bronze casting in Ancient China, Metallurgical Remains of Ancient China, Tokyo, 1976, 40.
15、山西省考古研究所:《侯马铸铜遗址》,文物出版社,1993年。
16、王工:《藏族古代技术文明及民族技术交流的研究》,中国科学院自然科学史研究所硕士论文,1988.年,43-47页。
17、转引自王工硕士论文,原图见 Dharampal, “Indian Science and Technology in the 18th century”,p224.
18、中国社会科学院考古研究所.:《殷墟的发现与研究》,科学出版社,2001年,89-90页。
19、陈光祖.:《殷墟出土金属锭之分析及相关问题研究》,《考古与历史文化-庆祝高去寻先生八十大寿论文集》(上),台北:中正书局,1991年, 355-392页。
20、万家保:《由殷墟发掘所见的商代青铜工业》,.《大陆杂志》,1979年,Vol.58,No.5,42页。
21、冯富根,王振江,华觉明等:《商代青铜器试铸简报》,《考古》,1980年1期,94页。
22、苏荣誉、华觉明、李克敏、卢本珊:《中国上古金属技术》,山东科学技术出版社,1995年,94页。
23、万家保:《由殷墟发掘所见的商代青铜工业》,.《大陆杂志》,1979年,Vol.58,No.5, 42页。
24、冯富根,王振江,华觉明等:《殷墟出土商代青铜觚铸造工艺的复原研究》,《考古》,1982年4期,536页。
25、洛阳市文物工作队:《1975~1979年洛阳北窑西周铸铜遗址的发掘》,《考古》,1983年5期,441页.
26、中国社会科学院考古研究所:《殷墟发掘报告(1958-1961)》,文物出版社,1987.年,21-22页。
27、石璋如:《殷代的铸铜工艺》,《历史语言研究所集刊》第26本。
28、华觉明:《商周青铜礼器铸后加工探讨》,《自然科学史研究》2007年3期,401-406页。
29、刘振群:《窑炉的改进和我国古陶瓷发展的关系》,中国硅酸盐学会编,《中国古陶瓷论文集》,文物出版社,1982年,163页。
30、刘可栋:《试论我国古代的馒头窑》,,中国硅酸盐学会编,《中国古陶瓷论文集》,文物出版社,1982年,176-178页。
31、中国硅酸盐学会编:《中国陶瓷史》,文物出版社,1982年,38页。
32、唐际根, The Social Organization of Late Shang China-A Mortuary Perspective, A Thesis Submitted to the University of London,2004.
33、张光直等:《商周青铜器与铭文的综合研究》,《中央研究院历史语言研究所专刊62,台北:中央研究院,1972年。
34、李亚农:《殷代社会生活》,上海:人民出版社,1955年,50页。
35、郭克煜、孙华铎、梁方建、杨朝明:《索氏器的发现及其重要意义》,《文物》1990年7期。
36、肖楠,《试论卜辞中的“工”与“百工”》,《考古》,1981年3期,266-270页。
37、黄盛璋:《试论三晋兵器的国别和年代及其相关问题》,《考古学报》1974年1期。
38、刘玉堂:《楚国手工业技术生产者的身份与地位》,《自然科学史研究》14卷2期,1995年。
2、李永迪, Anyang Foundry : Archaeological Remains, Casting Technology and Production Organization, A thesis for Ph. D to Harvard University,2003.
3、石璋如:《殷代的铸铜工艺》,《历史语言研究所集刊》第26本。
4、谭德睿:《中青铜时代陶范铸造技术研究》,《考古学报》1999年2期,220页。
5、李济、万家保:《殷墟出土五十三件青铜容器之研究》,1972年,台北。
6、刘煜:《殷墟青铜器制作工艺的技术演进》,《21世纪中国考古学与世界考古学》,中国社会科学出版社,2002年,613-631页。
7、华觉明:《中国古代金属技术铜和铁造就的文明》,大象出版社,1999年。
8、刘煜、岳占伟:《殷墟陶范的材料及处理工艺的初步研究》,,中国社会科学院考古研究所考古科技中心编《科技考古》第1辑,中国社会科学出版社,2005年,226-236页。
9、刘屿霞:《殷代冶铜术之研究》,《安阳发掘报告》第四期,1933年,681-696页。
10、中国社会科学院考古研究所编著:《殷墟的发现与研究》,科学出版社,1994年,87页。
11、河南省文物研究所:《郑州商代二里冈期铸铜基址》,《考古学集刊》第6集,中国社会科学出版社,1986年,100-122页。
12、洛阳市文物工作队:《1975-1979年洛阳西周北窑铸铜遗址的发掘》,《考古》1983年5期,430-441页。
13、熊海堂:《东亚窑业技术发展与交流史研究》,南京大学出版社,1995年,57页。
14、N. Barnard, Origins of bronze casting in Ancient China, Metallurgical Remains of Ancient China, Tokyo, 1976, 40.
15、山西省考古研究所:《侯马铸铜遗址》,文物出版社,1993年。
16、王工:《藏族古代技术文明及民族技术交流的研究》,中国科学院自然科学史研究所硕士论文,1988.年,43-47页。
17、转引自王工硕士论文,原图见 Dharampal, “Indian Science and Technology in the 18th century”,p224.
18、中国社会科学院考古研究所.:《殷墟的发现与研究》,科学出版社,2001年,89-90页。
19、陈光祖.:《殷墟出土金属锭之分析及相关问题研究》,《考古与历史文化-庆祝高去寻先生八十大寿论文集》(上),台北:中正书局,1991年, 355-392页。
20、万家保:《由殷墟发掘所见的商代青铜工业》,.《大陆杂志》,1979年,Vol.58,No.5,42页。
21、冯富根,王振江,华觉明等:《商代青铜器试铸简报》,《考古》,1980年1期,94页。
22、苏荣誉、华觉明、李克敏、卢本珊:《中国上古金属技术》,山东科学技术出版社,1995年,94页。
23、万家保:《由殷墟发掘所见的商代青铜工业》,.《大陆杂志》,1979年,Vol.58,No.5, 42页。
24、冯富根,王振江,华觉明等:《殷墟出土商代青铜觚铸造工艺的复原研究》,《考古》,1982年4期,536页。
25、洛阳市文物工作队:《1975~1979年洛阳北窑西周铸铜遗址的发掘》,《考古》,1983年5期,441页.
26、中国社会科学院考古研究所:《殷墟发掘报告(1958-1961)》,文物出版社,1987.年,21-22页。
27、石璋如:《殷代的铸铜工艺》,《历史语言研究所集刊》第26本。
28、华觉明:《商周青铜礼器铸后加工探讨》,《自然科学史研究》2007年3期,401-406页。
29、刘振群:《窑炉的改进和我国古陶瓷发展的关系》,中国硅酸盐学会编,《中国古陶瓷论文集》,文物出版社,1982年,163页。
30、刘可栋:《试论我国古代的馒头窑》,,中国硅酸盐学会编,《中国古陶瓷论文集》,文物出版社,1982年,176-178页。
31、中国硅酸盐学会编:《中国陶瓷史》,文物出版社,1982年,38页。
32、唐际根, The Social Organization of Late Shang China-A Mortuary Perspective, A Thesis Submitted to the University of London,2004.
33、张光直等:《商周青铜器与铭文的综合研究》,《中央研究院历史语言研究所专刊62,台北:中央研究院,1972年。
34、李亚农:《殷代社会生活》,上海:人民出版社,1955年,50页。
35、郭克煜、孙华铎、梁方建、杨朝明:《索氏器的发现及其重要意义》,《文物》1990年7期。
36、肖楠,《试论卜辞中的“工”与“百工”》,《考古》,1981年3期,266-270页。
37、黄盛璋:《试论三晋兵器的国别和年代及其相关问题》,《考古学报》1974年1期。
38、刘玉堂:《楚国手工业技术生产者的身份与地位》,《自然科学史研究》14卷2期,1995年。
本文曾发表于《文明探源通讯》16期
(责任编辑:高丹)